Author: Dan Maloney / Source: Hackaday
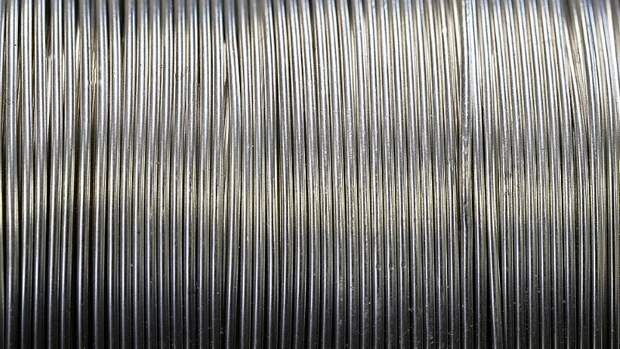
For most of the history of industrial electronics, solder has been pretty boring. Mix some lead with a little tin, figure out how to wrap it around a thread of rosin, and that’s pretty much it. Sure, flux formulations changed a bit, the ratio of lead to tin was tweaked for certain applications, and sometimes manufacturers would add something exotic like a little silver.
But solder was pretty mundane stuff.Then in 2003, the dull gray world of solder got turned on its head when the European Union adopted a directive called Restriction of Hazardous Substances, or RoHS. We’ve all seen the little RoHS logos on electronics gear, and while the directive covers ten substances including mercury, cadmium, and hexavalent chromium, it has been most commonly associated with lead solder. RoHS, intended in part to reduce the toxicity of an electronic waste stream that amounts to something like 50 million tons a year worldwide, marked the end of the 60:40 alloy’s reign as the king of electrical connections, at least for any products intended for the European market, when it went into effect in 2006.
Unintended Consequences
Whether the intention of EU regulators when adopting RoHS was to completely shake up the electronics industry is a moot point, because that’s pretty much what happened. The industry initially dug in its heels and made arguments against switching to lead-free solders, some of which were valid enough chemically and electronically to earn exemptions from RoHS. But lead-free solders, mostly tin with copper and silver mixed in, became the law of the land for most consumer electronic products.
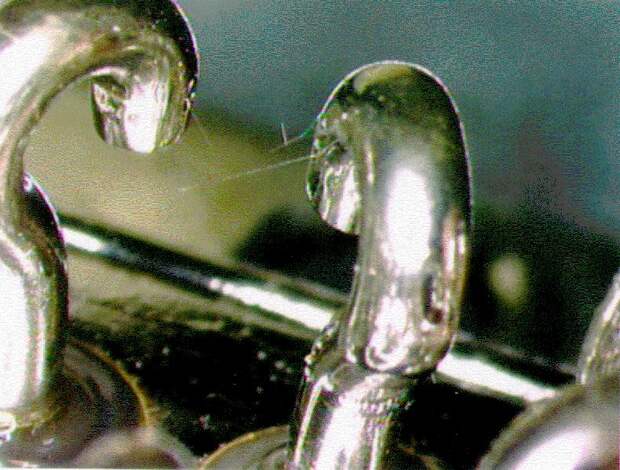
Despite the industry’s early predictions of doom from lead-free solders, manufacturers adapted to the changes well. Processes for wave soldering and reflow were changed, new flux chemistries were explored, and in general the predictions of a world gone haywire from the short-inducing…
The post Ask Hackaday: Get the Lead Out or Not? appeared first on FeedBox.